Plasma is very effective in removing the passive layer of a chromium oxide formed naturally on the surface of stainless steel, which is why UltraGlow® Ion Nitriding is used often to enhance the performance of stainless steel parts.
VIEW ARTICLES RELATED TO STAINLESS STEEL
UltraGlow Ion Nitriding Replaces Chrome Plating in Many Applications
Chromium and other metal nitrides formed in stainless steels have good thermal stability and maintain very high hardness at elevated temperatures to 1100ºF. Therefore, UltraGlow® Ion Nitriding replaces chromium plating in many applications (especially in the power-generation industry) where a nitrided layer does not peel off from the surface, as it often does with chrome plated parts, because there are no thermal expansion problems.
Mechanical Masking Stainless Steel
Also, mechanical masking is frequently used in many of these applications. The hardness of the nitrided layer in stainless steels is very high (> 70 HRC equivalent), but as in all AISI 300 series stainless steels, there is an abrupt change of hardness between the nitrided diffusion layer and the core (Figure 1).
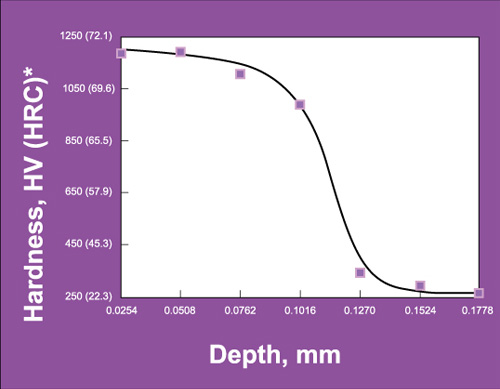
Hardness profile in UltraGlow® Ion Nitrided AISI type 304 stainless steel soot-blower tube. *Equivalent HRC, typical
View more articles related to heat treating stainless steel here.