posted
On Monday, July 1, 2024
in
Blog
Originally published by Hydraulics & Pneumatics on March 12, 2015 and authored by AHT employees. Click here to see the original content.
Environmental limitations on the usage of hex-chrome coatings¹ have yielded many alternative coatings and surface treatments for hydraulic and pneumatic cylinder piston rods. Piston rod surfaces need to have low coefficient of friction and resist wear from abrasion, erosion and sliding. But they also must be resistant to corrosion².
Destruction of the galvanically-plated chromium coatings, still used frequently, occurs through spalling. This disqualifies many engineering components from their applications. To the contrary, nitrided components typically develop corrosion spots, and although those can be cleaned off without affecting performance of the parts for a long time, they may still lead to premature failure. Enhancing corrosion resistance of the nitrided/nitrocarburized layers by post oxidizing is a significant step in further enhancing performance of the parts. We developed UltraOx® to meet and exceed those requirements.
The UltraOx treatment combines controllable ferritic nitrocarburizing (FNC) carried out either by gas or plasma method with post-oxidizing and proprietary impregnation step, all carried out in the same shop³. The technology is an alternative to other much more complex methods such as Melonite QPQ, Tenifer Q, Nitrotec and other processes²⁻⁴. UltraOx® has been developed using a new approach to the common problem by emphasizing microstructure-corrosion correlation⁵. Many actual and potential applications of the process are in the field of hydraulics and pneumatics.
Chromium Plating vs Compound Zone
Chromium plating can produce a monolithic layer on top of the steel component as shown in Figure 1A. The layer has significant hardness in the range of 800-900 HK (65-70 HRC equivalent) and it is plated over a comparatively soft steel base, Figure 1B. As it can be noticed, gradient of the hardness is very sharp at the surface and this may not be a very preferred stress profile in many applications. To the contrary, compound layer present in the nitrocarburized layer (Figures 2A and 2B) is supported by the diffusion zone, which exhibits a smooth transition of the hardness. Compound zone is not a coating like the chromium layer. To the contrary, it is formed by diffusion of nitrogen and carbon in the steel. Therefore, there is no problem with its adhesion to steel. It has been proven that the chromium-plated layer has micro-cracks, and because of that, flaking might occur if the direction of sliding is not perpendicular to the crack⁶⁻⁸.
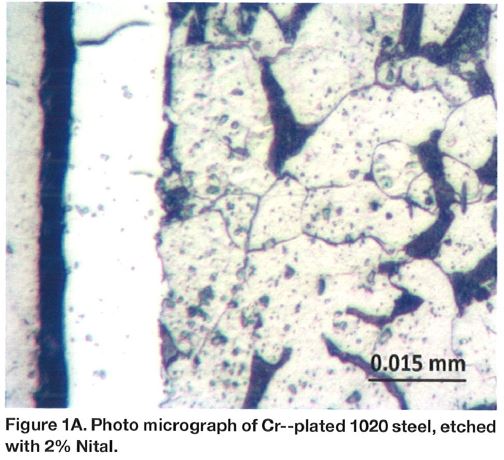
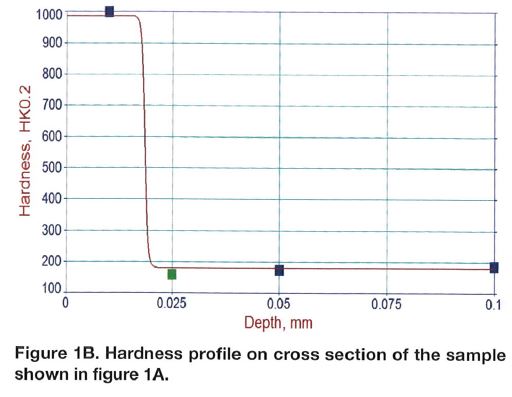
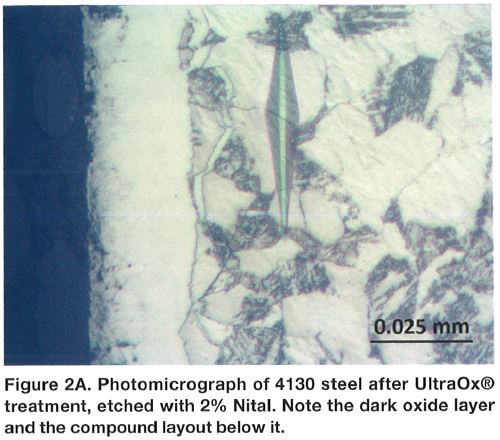
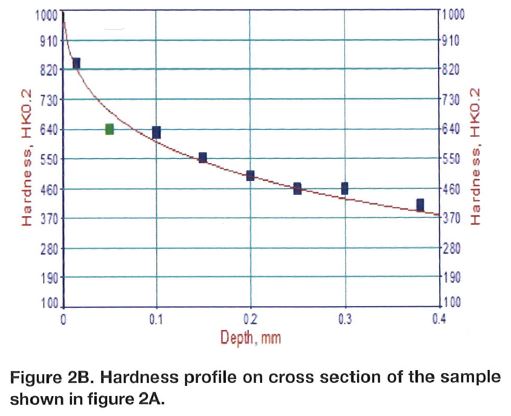
Black Finish with UltraOx
The UltraOx® treatment assures a very aesthetic look of the parts, Figure 3. The black appearance of the surface is achieved with a special post-oxidizing step carried out after FNC in the same furnace. In lieu of the color, the surface hardness of the component is significantly increased. This is extremely important since most of the failures start at the surface². It can be noted a multi-zone character of the near-surface region. The outer zone is built of Fe₃0₄ (magnetite), and the zone directly underneath is the two-phase compound zone. Both of these zones are saturated with the proprietary sealant during the post-impregnation step. Coating used for impregnating acts as an electrical barrier, protecting the interface solid-solution from electronic transfer of the species, i.e. protects from electrochemical reaction which is also called electrochemical corrosion. The zone below is very compact since it has iron-reach nitride containing less nitrogen than the intermediate, porous zone.
UltraOx Application Examples
UltraOx® is not only an environmentally-friendly process but also allows for uniform all-over treatment of the steel component. Therefore, it is more versatile than hard chromium plating, so there is no shadowing effect from connecting electrodes. Parts of any geometry can be treated. Some of the parts treated by Advanced Heat Treat Corp. are also of significant size, such as piston rods for skid-steer loaders and other off-highway equipment. Other parts are quite small and detailed, such as the outer tube for an industrial shock absorber, Figure 3. Durability of the UltraOx® layer is at least twice of the chromium plated coating. Many actual and potential applications of the process are in the field of hydraulics and pneumatics.
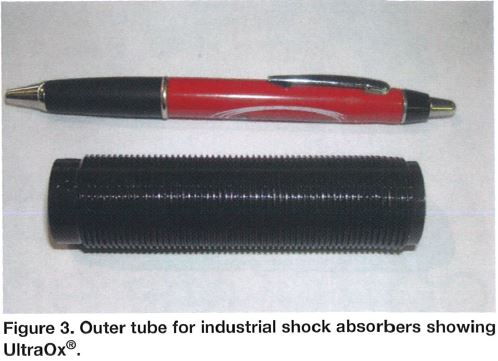
Want to learn more about switching from chrome plating to UltraOx? Click here.
References
1. EPA, Draft Toxicological Review of Hex Chromium: In Support of Summary Information on the Integrated Risk Information System (IRIS). 75 Fed. Reg. 60454 (2010), www.phoneline.com, May 2011.
2. J. Spies, Chapter 6 in E. J. Mittemeijer and J. Somers, Thermochemical Surface Engineering of Steels, Ed Woodhead Publishing, 2014.
3. M. Woods, UltraOx Treatment, Trade Name, 2012.
4. M. L. Doche, V. Meynie, H. Mazille, C. Deramix and P. Jacquot, Improvements of the corrosion resistance of low-pressure nitrided and post-oxidized steels by a polymer impregnation final treatment, Surface and Coatings Technology, 154, (2002), pp. 113-123.
5. J. A. Segui, Simulation-Led Strategy for Corrosion Prevention, Corrosion/Materials Science, Comsol News, 2014, pp. 36A-38A.
6. K. R. Newby, Industrial (Hard) Chromium Plating, Metals Handbook Vol. 5, Surface Engineering, Ed. ASM Intl. 1994, pp. 177-191.
7. Zhenkun Yanp, Alternatives to hard chromium plating on piston
rods.
8. M. Keshavarz Hedayat, Comparison of conventional and active screen plasma nitriding of hard chromium electroplated steel. Elsevier, 2009
- corrosion resistance
- ultraox®