posted
On Tuesday, February 1, 2022
in
Blog
Introduction
Scientists studying failure of various mechanical components did a significant analysis of various loadings and concluded that the most important are those which vary with time, i.e. fatigue as well as the phenomena which occurs during the process of friction. The latter are measured in most cases by the amount of wear and coefficient of friction [1 & 2]. Durability of such components is decided by surface layers which, depending on the type of technological process applied, may have a thickness of orders of 1 µm to several mm. The condition of the decisive surface layer is critical to wear resistance during the process of friction and to corrosion resistance. In the case of mechanical loading (especially fatigue resistance) as well as the action of corrosion (hydrogen corrosion), the critical role is played by the substrate, its condition and properties as well as the atomic relationship between the surface layer and the substrate. For this very reason, while considering life expectancy of machine components and assemblies, one should take into account the system: substrate-surface layer. Attributes to such a system are: thickness of the surface layer-ratio of this thickness to the entire cross-section, ratio of surface hardness to core hardness and the state of residual stresses, usually compressive within the surface layer, relative to the state of stresses in the substrate, which are usually tensile. An incorrectly applied surface layer may cause formation of a structural flaw in the transition zone of the layer and may lead to crack initiation, especially by the fatigue mechanism [1 & 2].
Wear & Bending Fatigue in Crankshafts
It was also concluded that bending fatigue as well as wear properties of steel components can be significantly improved when a compressive stress is induced at the surface [1-3]. It has been known that crankshafts get the maximum stress level at the pin fillet radius; therefore, hardening of this area has a special importance.
For those reasons, nitriding has been noted as a perfect surface hardening technology for enhancing performance and durability of many types of crankshafts used in the race cars industry and in military as well as the aviation industries for light-plane engines. This opinion has been based on the fact that the process of nitriding is carried out at low temperatures of 480-550° C (896-1022° F), well below tempering temperature of the steel. It has to be appreciated how important for durability of those crankshafts is proper steel composition as well as its prior nitriding heat treatment [4].
Unfortunately, the gas nitriding used in the older time and carried out in the gaseous ammonia was without a good method of controlling physico-chemical parameters of the surface reactions. The process was controlled by the dissociation rate of ammonia using just the simply instrument-water burette [5]. As a result, gas nitriding usually produced a layer often with the excessive thickness of the compound zone (called also white layer) which had a presence of the Epsilon-type Fe2-3N hexagonal nitride. This zone, because of its brittle and porous structure, had to be reduced/removed by grinding which significantly increased the cost of manufacturing.
Controllable Compound Zone with Ion Nitriding
Development of ion/plasma nitriding in 60’s and 70’s opened a possibilities for producing layers with limited thickness of the compound zone. This has been possible since ion nitriding is a “low-nitriding potential” process by its very nature and allows to produce a layer with a thin compound zone or avoid its formation at all without any excessive control of the physico-chemical parameters [5]. A high competition from the ion/plasma nitriding resulted in intense research in the field of gas nitriding and this process was modified and re-developed allowing to predict the outcome very precisely and to produce layers with a very thin compound zone or without it [5 & 6].
Layers with the compound zone thickness 0.005-0.010 mm (0.0002-0.0004”) can be now produced very consistently using both, well-controlled gas and ion nitriding methods, see Fig. 1 and Fig. 2.
Figure 1
Photo micrograph of the ion nitrided 4340 sample. Nitrided temperature 520° C. Etched with 3% nital. White layer on the left is the ɣ’-Fe4N nitride.
Figure 2
Point-to-point hardness profiles of 4340 steel samples plasma and gas nitrided for the same length of time at 520° C (986° F).
Minimizing Tensile Stress in Crankshafts
The nitrided layer is under compression and therefore has a very positive effect on fatigue life of the components, such as crankshafts by improving their bending strength during the cycling. This is a result of minimizing tensile stress at the surface and moving it below by distance X indicated in Fig. 3.
Figure 3
Schematic diagram showing effect of residual stresses from nitrided layer on the final stress distribution of the shaft subjected for rotational bending. Adopted from T. Bell [3]. Note distance X showing position of the stress below the surface and its maximum value.
Also, the ability to form nitrided layer with the ɣ’ (Fe4N) compound zone was a major step in improving bending fatigue properties of the crankshafts. This phase is much more elastic than the Epsilon phase with the higher nitrogen content. However, the compound zone of limited thickness might be needed in certain situations for reducing adhesive forces and reducing friction of the bearing journals or enhancing corrosion protection.
Gas Nitriding: All-Over Hardening or Masking?
The gas nitriding process allows for the allover hardening of the entire component and therefore some of the crankshaft surfaces, which are machined after nitriding for its final balancing must stay soft and they need to be mask off with a masking paint or galvanically deposited copper to prevent nitriding, Fig. 4.
Figure 4
Lot of a typical racing cars crankshafts after UltraGlow Gas nitriding. Picture taken at Advanced Heat Treat Corp. Monroe, Michigan. Green-color areas of the parts were masked off with the masking paint.
Mass produced crankshafts are made of cheaper steels and they are very often successfully nitrocarburized for improving their fatigue and wear resistant [7].
LEARN ABOUT NITROCARBURIZING HERE
Ion/Plasma Nitriding: Best Heat Treatment for Crankshafts
The ion nitriding method has been considered by many as the best way of surface hardening used for all types of crankshafts [6 & 8]. The method allows for producing nitrided layers with the ɣ’-Fe4N nitride and it has an easiness in mechanical masking of selected areas of the crankshafts such as oil holes, keyways and threads. The process is carried out in a vacuum-type glow discharge chamber where the parts have cathodic polarization and the vessel is anodic. Environment-friendly atmosphere of nitrogen mix with hydrogen is used [6]. Temperature of the crankshafts is measured with a thermocouple inserted in one of them, see Fig. 5.
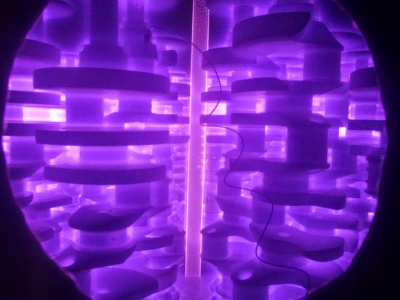
Figure 5
UltraGlow Ion nitriding of high performance crankshafts. Picture taken at Advanced Heat Treat Corp. Monroe, Michigan.
|
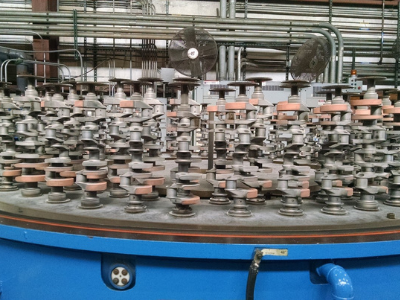
Figure 6
Lot of the high-performance crankshafts after UltraGlow Plasma/ion nitriding. Note mechanical masking plates at tops of the crankshafts and a red-looking areas masked off with the paint. Picture taken at Advanced Heat Treat Corp. Monroe, Michigan.
|
Sometimes combination of mechanical- and painting masking has to be used to protect certain areas of the crankshaft from nitriding, see Fig. 6.
UltraGlow Ion Nitriding Process for Crankshafts
UltraGlow Ion Nitriding has been used very successfully for nitriding of many types of crankshafts including those for larger Diesel engines. Parts like that are processed individually in a very special vertical vessels allowing for preservation of the dimensional stability of the part. Each part is tested for surface hardness with a portable hardness testers with maximum load of 1 KG. Samples run in different positions of the load are tested in our laboratory for reporting to the customer exact data regarding structure details, as thicknesses of the diffusion and compound zone layers. The part is packed and shipped.
Advanced Heat Treat Corp is in possession of many ion and gas nitriding vessels allowing us to process any size and shape crankshafts without limitations regarding the material of these parts.
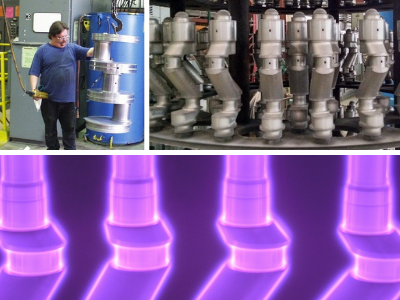
Fig. 7. Examples of various crankshafts processed at Advanced Heat Treat Corp. Monroe, Michigan.
Have Questions about Heat Treating Crankshafts and Other Applications?
CONTACT US
References
1. Nakonieczny A., 1984, Podwyzszenie wytrzymalosci zmeczeniowej czesci maszyn przez obróbki cieplnej i powierzchniowe¡ obróbki plastycznej (Enhancement of fatigue strength through heat treatment and surface work hardening), Proc. XXIV Seminar IMP, XI on Metallurgy and Heat Treatment, Warsaw, IMP, Warsaw, 49-52.
2. A. Nakonieczny, “Fatigue fracture of nitrided and carbonitrided layers”, JOURNAL OF THEORETICAL AND APPLIED MECHANICS 44, 3, pp. 713-730, Warsaw 2006.
3. T. Bell and N.L. Loh, “The Fatigue Characteristics of Plasma Nitrided Three-Percent Cr-Mo Steel”, J. Heat Treating, Vol. 2 No. 3, June 1982, pp. 532-537.
4. Machine Design, News, 2005, 47, August,
5. J.-M. Winter and J. Kalucki, “Gas Nitriding and Gas Carburizing of Steels”, ASM, Handbook, Volume 4A, Steel Heat Treating Fundamentals and Processes, J. Dossett and G.E. Totten, editors, pp. 647-679.
6. E. Rolinski,” Plasma Assisted Nitriding and Nitrocarburizing of Steel and other Ferrous Alloys”, Chapter 11 in Thermochemical Surface Engineering of Steels, Ed. E. J. Mittemeijer and M. A. J. Somers, Pub. Woodhead Publishing, 2014, pp 413-449.
7. Tetsuya Asai, Yoshihiro Takitani, Naoyuki Sano and Hitoshi Matsumoto, “Strength Enhancement of Nitrocarburized Crankshaft Material”, SAE Int. J. Mater. Manuf. Vol 1, Issue 1, pp. 204-210.
8. E. Rolinski, G. Sharp, “When and Why Ion Nitriding/Nitrocarburizing Makes Good Sense”, Industrial Heating, Aug. 2005, pp 67-72.
Who is Doctor Glow?
Dr. Edward Rolinski, aka Doctor Glow, has been studying the plasma/ion nitriding phenomenon since the 1970s and is arguably one of the most knowledgeable people in North America when it comes to nitriding.
The doctor has written countless articles and whitepapers in industry publications and manuals. Some of his most noteworthy contributions include the chapter on "Controlling Plasma Nitriding" in ASTM International (2017) as well as "Nitriding of Titanium Alloys" in the ASM Handbook (2016).
Dr. Edward Rolinski is the Senior Scientist at Advanced Heat Treat Corp. (AHT) and has been employed at AHT since 1994.
LEARN MORE ABOUT DOCTOR GLOW VIEW HIS RECENT ARTICLES
- automotive
- edward rolinski
- ferritic nitrocarburizing
- gas nitriding
- ion nitriding
- nitrocarburizing
- plasma nitriding