posted
On Wednesday, July 19, 2023
in
Blog
UltraGlow® Ion Nitriding, the glow discharge plasma process, is very effective when applied to components made of various stainless steels [1]. The process is carried out in a vacuum chamber where the glow discharge is initiated between the load/cathode and the vessel wall/anode, Fig. 1.
Fig. 1. Schematic representation of plasma nitriding equipment with two alternative additional heating sources; cathodic shields or resistance heating elements
The treatment is well-suited for nitriding parts at low or high temperatures. Ion bombardment activates the surface of the stainless steels without any additional entry procedures like those needed before gas nitriding. During the plasma nitriding process, the energy of ions and neutrons bombarding the cathode-work piece is sufficient not only to remove the native oxides of chromium or other elements passivating the surface, but also to cause significant sputtering of the alloy, Fig. 2.
Fig. 2. Surface reactions in ion nitriding
This fact, together with a low partial pressure of nitrogen in plasma, is of a paramount importance in limiting the compound layer thickness, enabling us to call plasma nitriding a low-nitriding potential process [1]. With such a thin compound layer, the nitrided zone, i.e. diffusion zone and compound layer together, is under residual compressive stress. This is required for enhancing bending fatigue properties, Fig. 3.
Fig. 3. Effect of nitrided layer on stress distribution in rotary bending shaft after T. Bell [2].
Nitrided stainless steel components are often used where resistance to friction and bending fatigue at elevated temperatures is required (Roliński et al, 2005). High hardness of the nitrided layer is maintained under those conditions since nitrides of Cr-Mo-Ti are thermally very stable. Another benefit is the ability to selectively heat treat the application with use of mechanical masking, protecting chosen areas from the ion nitriding process such as areas that may need to be welded post-nitriding or bores that cannot have growth . [1-3], see Fig. 4.
Fig. 4. Mechanical masking of threaded holes in gas compressor cylinders. Picture taken at Advanced Heat Treat Corp. in Monroe, Michigan.
Nitriding of Stainless Steels
Duplex Stainless Steels
All types of stainless steels can be ion nitrided. It should be noted that the low-temperature treatments are used when a formation of the expanded austenite structure layer is preferred as such made of the duplex stainless steels. This structure is good for improving corrosion resistance of the steel with a significant increase of its surface hardness, Fig. 5.
Fig. 5. Optical photomicrograph of 2205 duplex stainless steel sample ion nitrided. Note conversion of ferrite grains into austenite at surface of the sample. Etched with Marbles.
Austenitic Stainless Steels
Low nitriding temperatures are used when a formation of the expanded austenite, corrosion resistant layer is required. Higher nitriding temperatures are used when a formation of the hard and thicker layers are required and their corrosion resistance has a secondary importance. It should be noted that nitriding affects properties of austenitic stainless steels such as surface hardness, corrosion resistance as well as their magnetic properties [1, 3]. However, when the steel is nitrided at a very high temperature, above 700°C (1292°F) its paramagnetic properties can be preserved, Fig. 6.
Fig. 6. Effect of nitriding temperature on content of magnetic phases and surface hardness of austenitic stainless steel; initial state 0% of magnetic phases, 286 HV5 [3].
Examples of ion nitriding applied to austenitic stainless steel parts are shown in Fig. 7 and 8. The benefits of this process can be summarized here as the ease of surface activation by ion bombardment and mechanical masking to protect certain surfaces from hardening.
Fig. 7. Ion nitriding of turbocharger arms and shafts. Pictures taken at Advanced Heat Treat Corp. Waterloo, Iowa.
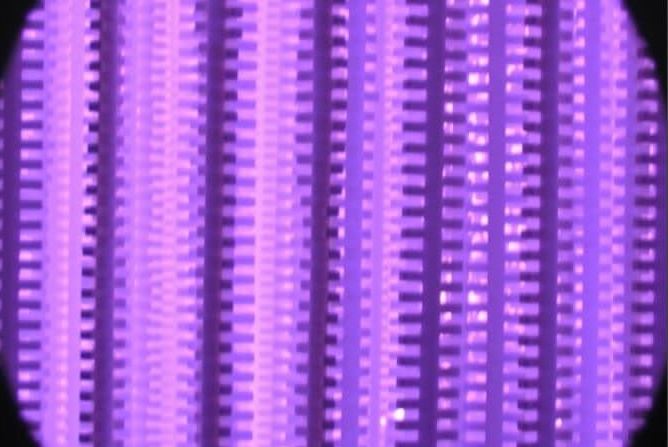
Fig. 8A. Precision parts made of 310 SS under plasma glow, a). Inside diameter holes are protected from the treatment and used for fixturing
|
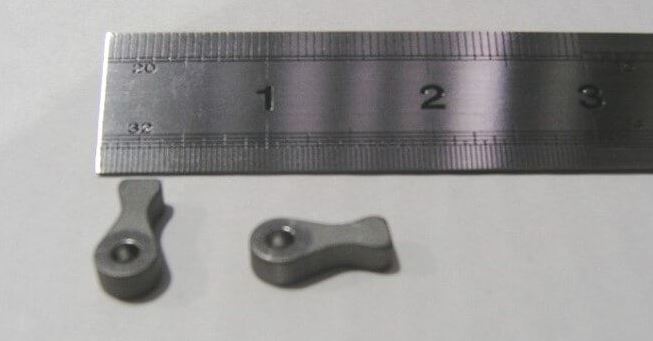
Fig. 8B. Large volumes can be processed in a single batch. The case depth is 0.002” min. and hardness >900 HV.
|
Precipitation Hardenable (PH) Steels
The thickest layers are formed in the regular ferritic and martensitic 400’s stainless steels. Precipitation hardenable austenitic or martensitic stainless steels require consideration of their aging temperatures during the nitriding process, and therefore, the layers produced are thinner [1,3,4]. The hardness achieved in high-strength steels such as precipitation hardenable 17-4PH with 1170 MPa (170 ksi)-yield strength or A-286 is very high. The latter iron-base superalloys are useful for applications requiring high strength and corrosion resistance at elevated temperatures. Specific uses include jet engine nacelles, parts, and fasteners. On many occasions, these steels also need increased wear and fatigue resistance which are significantly enhanced by ion/plasma nitriding [1-2]. Example of the 17-4PH pins during ion nitriding is shown in Fig. 9.
Fig. 9. Ion nitriding of the 17-4PH pins. Picture taken at Advanced Heat Treat Corp. in Monroe, Michigan.
These types of steels nitride to a very high hardness level while maintaining core hardness/yield strength of the treated components. Nitriding temperature has to be much below the aging temperature of the steel to avoid unwanted structural and dimensional changes of the treated components. Thanks to that, a very high strength of the steel, demonstrated with the high core hardness can be maintained, Fig. 10 & 11.
Fig. 10. Hardness profile of ion nitrided precipitation hardenable 17-4 PM martensitic steel. Note a very high core hardness of the steel and a very sharp change of the hardness at the end of the nitrided layer
Fig. 10B. Photo micrograph of the ion nitrided precipitation hardenable 17-4 PM martensitic steel. Note a very sharp change of the structure at the end of the nitrided layer. Etched with 3% Marbles
Fig. 11A. Hardness profile of the ion nitrided of precipitation hardenable A-286 austenitic steel after long nitriding cycle. Note a very high core hardness of the steel and a very sharp change of the hardness at the end of the nitrided layer
Fig. 11B. Photo micrograph of the ion nitrided precipitation hardenable A-286 austenitic steel. Note a very sharp change of the structure at the end of the nitrided layer. Etched with 3% Nital.
Powder Metal (PM) Stainless Steels
Plasma has a limited ability to penetrate porosities and cavities present in a low-density sintered metal products and surface cracks [1]. As a result, plasma nitriding creates smooth surface layers in those materials. In contrast, gases or salts can penetrate those materials below the surface, causing internal or locally deeper nitriding. This may produce embrittlement or roughening of the surface treated products. Cast as well as powder metal 310/321 stainless steels can be ion nitrided to a case depth of 0.005” and a hardness of above 60 HRC equiv., see example of the structure in Fig. 12. This is an extremely important application of the ion nitriding process, since the gas nitriding methods may embrittle the PM structure by penetrating internal structure with ammonia [5].
Fig. 12. Structure of the turbocharger unison rings made of a low-density PM 310 stainless steel after plasma nitriding. Etched with 3% Nital.
The ability to nitride stainless steels’ components to the highest technical standards is a benefit of the ion nitriding process. The process is also environmentally-friendly with limited usage of (non-poisonous) gases.
Interested in Learning More About Nitriding Stainless Steel? Check out more of our articles.
VIEW OTHER STAINLESS STEEL ARTICLES.
"Ion Nitriding Stainless Steels - Powder Metal, Austenitic, Precipitation Hardenable & Duplex" References
1. E. Rolinski,” Plasma Assisted Nitriding and Nitrocarburizing of Steel and other Ferrous Alloys”, Chapter 11 in Thermochemical Surface Engineering of Steels, Ed. E. J. Mittemeijer and M. A. J. Somers, Pub. Woodhead Publishing, 2014, pp 413-449.
2. T. Bell and N. L. Loh, “The Fatigue Characteristics of Plasma Nitrided Three Pct. Cr-Mo Steel”, J. Heat Treating, Vol. 2. No3, June 1982, pp 232-237.
3. E. Rolinski, “Effect of plasma nitriding temperature on surface properties of stainless steel”, Surface Engineering, 3(1987) 35-40.
4. E. Rolinski, A. Springer and M. Woods, “PRACTICAL ASPECTS OF PLASMA NITRIDING KINETICS FOR 17-4 PH STAINLESS STEEL”, Advanced Materials and Processes, 2022, July/August, 56-59.
5. E. Rolinski, G. Sharp, “Ion Nitriding and Nitrocarburizing of Sintered PM Parts”, Industrial Heating, Oct. 2004, pp 33-35.
- ion nitriding
- nitriding
- plasma nitriding
- powder metal
- precipitation hardening
- stainless steel