posted
On Monday, November 1, 2021
in
Blog
What is Ion Nitriding?
The process of ion nitriding is carried out under vacuum conditions in a cold-plasma DC glow discharge environment where the treated object has cathodic- and the wall of the vessel has anodic- polarization. See Fig. 1.

Fig. 1. UltraGlow ion nitriding of large steel molds. Cathodic glow covers the entire surface and the threaded holes are masked off with the bolts. The tube at the center is the central anode used for enhancing the glow discharge uniformity.
Active nitrogen species are produced at the cathode surface and react with it, forming the nitrided layer. The heat is generated by the glow discharge in cold-wall type vessels. In hot-wall type vessels, in addition to the glow discharge heating, heat is also delivered from the resistant heating elements located in a wall of the vessel. In either type of vessel, impact of the ions and neutrals with the cathode (part or component) causes sputtering of its surface. This process activates even the most difficult to nitride stainless steels and alloys.
What Allows the Masking to Be So Effective?
Knowledge of the mechanism of the ion nitriding is very important since it allows for proper usage of plasma to utilize its tremendous benefits stemming from its unique characteristics [1-5]. In ion nitriding, all the high-energy ions are formed near the cathode and are accelerated toward it in the Crookes Dark Space (CDS). See Fig. 2. The ions and neutrals impact the cathodic surface with energy reaching up to 200 eV [1]. The energy of the ions depend on the thickness of the CDS, which at lower pressure, becomes larger, allowing for their acceleration. Higher pressure increases the quantity of the ions, which increases plasma density and the total number of active species.

Fig. 2. Near cathode glow discharge showing cathodic glow, CDS, and negative space zones.
The prevailing species bombarding the cathode are ions (N2+, N+, NxHy+, H2+, H+) and neutrals, which are the same species as ions with the same energy but without a charge [1]. All the energetic species colliding with the cathode form active nitrogen atoms N* which are chemisorbed at its surface and diffused into the metal (steels, titanium, etc.) causing the formation of the nitrided layer. This process allows nitriding to be limited only to the areas bombarded by ions and neutrals. Therefore, mechanical protection from the hardening of threaded or small holes, sharp corners, etc. is done simply by eliminating direct contact of the plasma with mechanical masking of the selected area, Fig. 3.
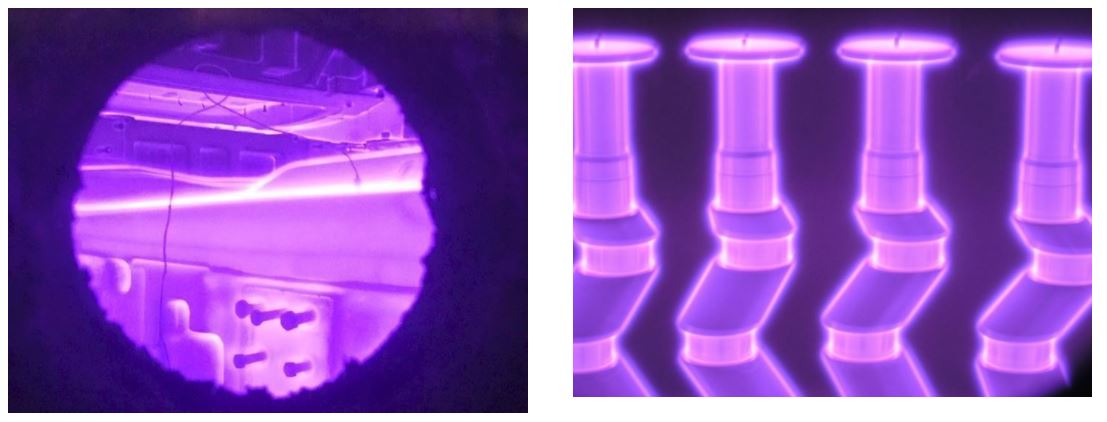
Fig. 3 & 4. Ion nitriding of the and stamping dies (left ) and crankshafts (right). Note masking plates at the top of the cranks for protecting the threaded holes from nitriding and bolts masking threaded holes in the dies.
Sputtering is a phenomenon often accompanying ion nitriding. Most of the species impacting the cathode have sufficiently high energy to cause this phenomenon and therefore, the process is known for its effectiveness in the removal of the native oxides present at the surface of stainless steels. Therefore, nitriding without any special activators, like those which have to be used in gas nitriding, can be carried out.
Some low-density powder metals (PM) can suffer from the excessive presence of NxHy+ and neutrals in plasma which may cause locally deeper penetration of the layer. However, proper control of the process allows for eliminating those effects [5].
Ion nitriding is a very efficient process and it uses very small amounts of gases such as nitrogen and hydrogen, occasionally with a small percentage of hydrocarbons. Flow rates are typically around a few hundred liters (10 gallons) per hour for a 160” diameter vessel. No poisonous or harmful gases are used in this process so it is incredibly environmentally friendly.
Ion nitriding is a low-nitriding potential process by its nature. With proper knowledge of the process, there is never reason to worry about the compound zone (CZ) formation becoming too thick, which is the main problem in other nitriding techniques. The ease of limiting CZ thickness is partially due to the sputtering mechanism, which is microscopically removing material while forming new CZ. Additionally, the low partial pressure of nitrogen is another factor preventing the formation of too many active nitrogen species. Both of these factors reduce the excessive thickness in the CZ formation [1, 4].
Ion Nitriding: A Solution for Bending Fatigue, Fractures, Corrosion & More
Applications of ion nitriding are numerous. The process is specifically useful when a quick and very effective local masking/protection from nitriding is needed, as mentioned above. Also, for typical processing scenarios, the compound zone produced on the surface is easily limited to prevent excessive thickness or brittleness. This makes it a very useful process for all applications where bending fatigue properties or fracture toughness of the component need to be improved.
Stainless steel components are very often ion nitrided when their tribological or bending fatigue performance needs to be enhanced. In situations like that, typically the process is carried out at 950-1080° F. If corrosion resistance needs to also be improved, the process is carried out at a very low temperature, about 740-780° F for forming the expanded austenite phase containing nitrogen and/or carbon. Corrosion resistance of carbon or low-alloy steel is improved because the CZ that forms at the surface is very dense and protects the iron atoms in the steel from oxidation/corrosion.
Surface hardening of the low-density PM components is very often realized by using the ion nitriding process since it is the only process guaranteeing the formation of the hard nitrided layer without risking embrittlement of the product. Other diffusion processes, specifically gas nitriding, very often result in the internal hardening of PM components, which is typically undesirable. This is due to the ability of ammonia molecules (gas nitriding) to penetrate deeply in the porous structure of PM components, causing hardening throughout the components' thickness.
Availability of long vertical vessels at Advanced Heat Treat Corp allows us to process very big size parts requiring a uniform hard layer along the entire length. An example is shown in Fig. 4.

Fig. 4. Long steel bar during loading into ion nitriding vessel through the roof of the building at Advanced Heat Treat Corp in Monroe, Michigan.
Applications of ion nitriding are still growing because of its technical as well as environmental advantages over conventional surface treatment methods.
References
- E. Rolinski,” Plasma Assisted Nitriding and Nitrocarburizing of Steel and other Ferrous Alloys”, Chapter 11 in Thermochemical Surface Engineering of Steels, Ed. E. J. Mittemeijer and M. A. J. Somers, Pub. Woodhead Publishing, 2014, pp 413-449.
- E. Rolinski, G. Sharp, “When and Why Ion Nitriding/Nitrocarburizing Makes Good Sense”, Industrial Heating, Aug. 2005, pp 67-72.
- E. Rolinski, A. Konieczny, G. Sharp, “Nature of Surface Changes in Stamping Tools of Gray and Ductile cast Iron During Gas and Plasma Nitrocarburizing”, Journal of Materials Engineering and Performance, 2009, Vol. 18 No 8, pp 1052-1059.
-
E. Rolinski, G. Sharp, “Effect of Sputtering on Compound Zone Formation in the Plasma Nitriding of 3% Cr-Mo-V Steel”, Journal of Materials Engineering and Performance, 10(4)(2001) pp 444-448.
-
E. Roliński, M. Woods “Plasma Nitriding Mechanisms of Low-Density Sintered Metal Products/Mechanismen des Plasmanitrierens von gesinterten Metallprodukten mit niedriger Dichte”, HTM J. Heat Treatm. Mat. 76 (2021) 1, 2021, pp. 58-63.
- edward rolinski
- ion nitriding