posted
On Tuesday, November 15, 2022
in
Blog
Gas as well as liquid or plasma/ion nitriding are thermochemical processes used to improve the surface of ferrous alloy components for applications requiring high wear/tribological and corrosion resistance properties [1-10]. When the nitrided layer is properly structured, it also improves rolling contact or bulk/volume bending fatigue life [1, 2].
Nitriding doped with carbon is called Ferritic Nitrocarburizing or FNC. Estimations suggest that FNC is about 60-70% of all nitriding-related processes. It should also be mentioned that FNC is typically carried out in a temperature range between 540-580° C (1004-1076° F) although some processes, especially those carried out in salts, exceed this upper temperature and some, when plasma is involved, can be done at much lower temperatures. Plasma allows the activation of hydrocarbon gases regardless of the processing temperature. Both gas and plasma FNC end with a slow cooling.
FNC Compound Zone
Efficiency of the nitrided layer’s modification with the carbon is very important for enhancing properties of the compound zone (CZ) formed at the top of the nitrided layer. Carbon presence in the ε-Fe2-3N(C) CZ affects its thickness as well as its hardness and anti-corrosion properties. The majority of steels treated with FNC are low-carbon and/or low alloy steels. Hardness of the diffusion zone (DZ) in plain carbon steels is not very high, Fig. 1. Therefore, it is very important to produce CZ with proper phase composition and thickness. Typically, CZ produced with FNC has a thickness of 0.010- 0.030 mm (0.0004-0.0012”) and its hardness in plain carbon steel is >55HRc equivalent or >550 HV. Hardness of CZ in alloyed steels is much higher.
Figure 1
Hardness profile in 1018 steel after FNC treatment at 1058° F at Kn=3 for 3 hours. Note much higher hardness of CZ at the surface than hardness of the diffusion zone.
|
.png)
Figure 2
Photomicrograph of 1018 steel after FNC process showing a typical compound zone. Etched with 3% Nital.
|
Nitrogen & Carbon's Effect on Corrosion Resistance
It was proven that nitrogen and carbon content in the ε compound zone has the most important effect on its corrosion resistance [4]. Optimum value for corrosion resistance in 0.9 m NaCl electrolyte is when the concentration ratio [C]/[N+C] is between 0.05-0.2 and the sum of both elements should be above 8 wt. % [4]. A microphotograph showing a typical CZ produced by FNC process of 1018-low carbon steel is shown in Fig. 2. It should be noted that the outer portion of CZ has a porous zone, which should be controlled [1]. Such zones are sometimes needed for retaining lubricants in the surface.
On occasions, steels for fast machining, containing sulfur such as 1215, are FNC-treated. In situations when there are significant post-machining stresses in the surface of those steels, a pre-FNC recrystallize-anneal or stress relieving is needed and after that the CZ is very uniform after the treatment, see Fig. 3. In carbon steels, precipitates of ɣ’-Fe4N nitrides are visible below the compound zone. Deeper areas of the diffusion zone also contain Fe16N2 nitrides, Fig. 4. Presence of both nitrides is the effect of smaller solubility of nitrogen in plain carbon steels. In alloy steels, nitrogen dissolves to a higher percentage and forms only very fine alloy-nitrides not visible by the optical microscopy.
Figure 3
Microstructure of 1215 steel after recrystallize-anneal and FNC. Etched with 3% Nital. Note precipitates of ɣ’-Fe4N nitrides below compound zone.
|
Figure 4
Photomicrograph of the diffusion zone in 1008 steel after FNC. Etched with 3% Nital. Note precipitates of nitrides; larger ɣ’- Fe4N and smaller ɣ”-Fe16N2 phase.
|
FNC with Post Oxidizing
Further enhancement of corrosion properties can be achieved with the post-oxidizing step/process used after nitriding. It has been proven that the post-oxidizing step, added at the end of the FNC cycle, further increases corrosion resistance of the nitrided layer by forming a thin Fe3O4 iron oxide known as the Magnetite [2, 4], Fig. 5.
Figure 5
SEM microstructure of 4140 steel after plasma FNC and post oxidizing. Black layer at the surface is a layer of Magnetite.
This 1-3 µm thick oxide may also increase the outer hardness of the layer [2]. The physical appearance of the treated product also becomes very attractive because of the black color of the oxide, see Fig. 6 & 7.
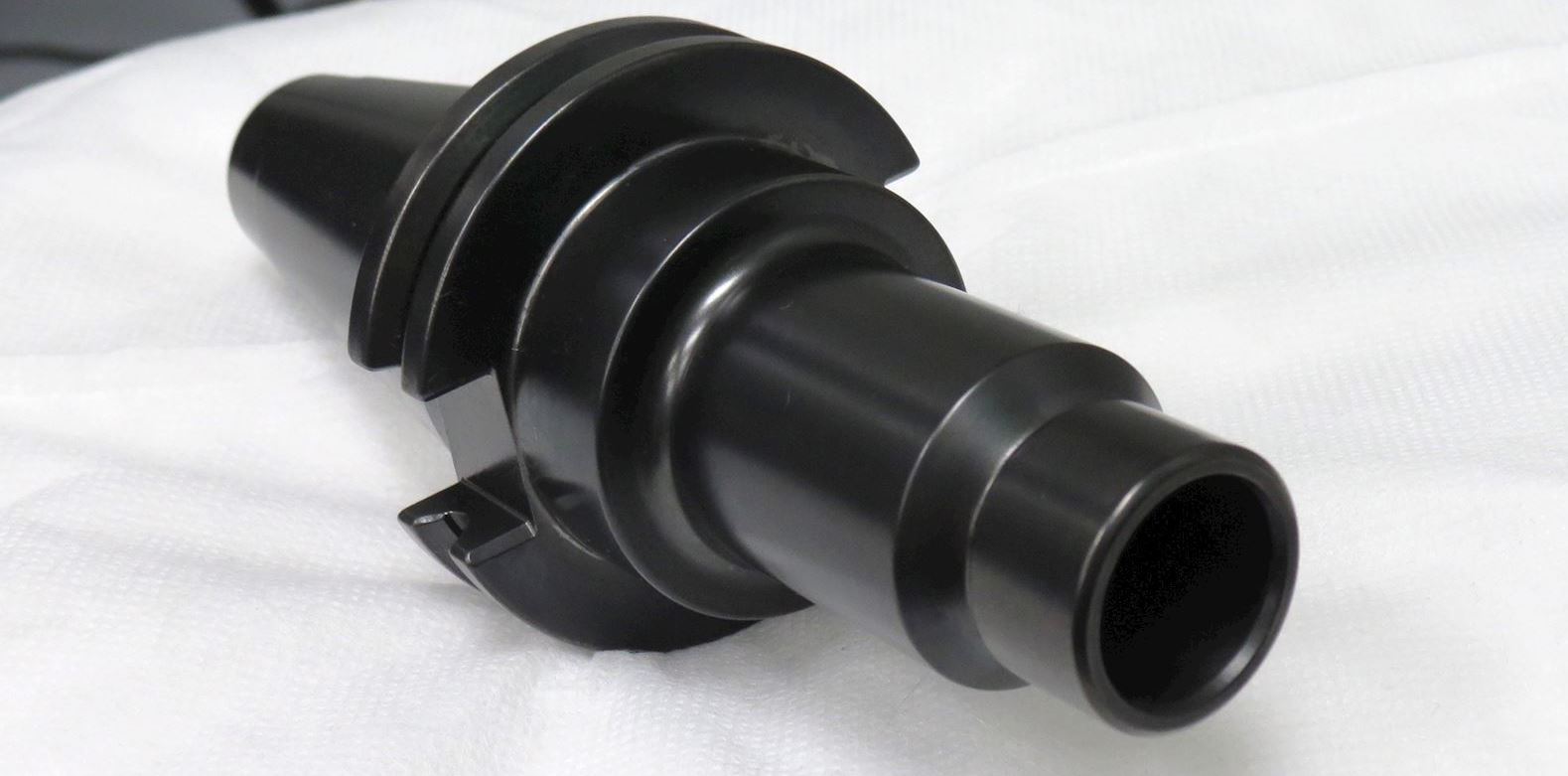
Figure 6
Salt spray tests carried out at Advanced Heat Treat Corp. demonstrated that low carbon steel parts treated with our UltraOx technique lasted over 400 hours without showing any signs of corrosion.
Learn More About Ferritic Nitrocarburizing (FNC) & Its Effect on Wear & Corrosion by visiting our webpage.
VIEW FNC SERVICE PAGE
References
1. Automated Gaseous Nitriding Controlled by Potentials, AEROSPACE MATERIAL SPECIFICATION, AMS2759TM/12, SAE INTERNATIONAL, REV. B Revised 2018-07.
2. H. J. Spies.; A. Dalke, “Case Structure and Properties of Nitrided Steels”. In Comprehensive Materials Processing; Krauss, G., Ed.; Elsevier Ltd., 2014; Vol. 12, pp 439–488.
3. E. Rolinski,” Plasma Assisted Nitriding and Nitrocarburizing of Steel and other Ferrous Alloys”, Chapter 11 in Thermochemical Surface Engineering of Steels, Ed. E. J. Mittemeijer and M. A. J. Somers, Pub. Woodhead Publishing, 2014, pp 413-449.
4. H-J. Spies, “Corrosion behavior of nitrided, nitrocarburized and carburized steels”, Thermochemical Surface Engineering of Steels”. pp 267-308. http://dx.doi.org/10.1533/9780857096524.2.267, Copyright © 2015 Elsevier Ltd.
5. K.-M. Winter J. Kalucki, “Gas Nitriding and Gas Nitrocarburizing of Steels”, ASM Handbook, Vol. 4A, Steel Heat Treating Fundamentals and Processes, J. Dossett and G.E. Totten, editors, 2013 ASM International, pp.647-679.
6. L. Małdzinski.: Z. Przyłęcki, J. Kunze, “Equilibrium between ammonia-hydrogen mixtures and the ε-phase of iron, Steel Research, 1986, Vol. 57, 12, p. 645-649.
7. J. Kunze, “Nitrogen and Carbon in Iron and Steel Thermodynamics”, Phys. Res., Vol 16, Akademie-Verlag, Berlin, 1990.
8. M.A.J. Somers and E.J. Mittemeijer, “Model Description of Iron-Carbonitride Compound-Layer Formation during Gaseous and Salt-Bath Nitrocarburizing”, Mater. Sci. Forum, Vol 102–104, 1992, p 223–228.
9. M.A.J. Somers, “Thermodynamics, Kinetics and Microstructural Evolution of the Compound Layer; A Comparison of the States Knowledge of Nitriding and Nitrocarburizing”, Heat Treat. Met., Vol 27 (No. 4), 2000, p 92–102
10. J. Senatorski, J. Tacikowski, E. Rolinski and S. Lampman, “Tribology of Nitrided and Nitrocarburized Steels”, ASM Handbook Vol 18, Friction, Lubrication and Wear Technology, ed. G. Totten ASM International, 2017, pp.638-652.
- cast iron
- ferritic nitrocarburizing
- nitrocarburizing
- ultraox®