posted
On Wednesday, April 27, 2022
in
Blog
Nitriding has an old history of development and applications. It has been used for more than 100 years to improve wear and corrosion resistance as well as fatigue strength in many engineering components made of steels or cast irons [1-8]. This process was modified and enhanced very quickly by introducing carbon-bearing gases to the atmosphere and causing alloying of the upper portion of the hardened layer, resulting in even better properties of the layer. In this way, nitrocarburizing was introduced. The precipitation of nitrides and carbonitrides as well as the nitrogen supersaturation of the ferrite, respectively, cause an increase in surface hardness and generation of compressive residual stresses [3].
Depending on the specific application, the process can be adjusted to produce a layer with the proper structure required for it. The nitrided layer has essentially two sublayers; the compound zone (CZ) at the surface also called white layer (WL) and below, a layer formed by nitride precipitations called the diffusion layer (zone), see Fig. 1.
Figure 1
Photomicrograph of ion nitrided Caldie Cast material showing components of the layer, etched with 3% Nital.
In alloyed steels, the diffusion zone is very hard as can be seen in Fig. 2.
Figure 2
Hardness profile in nitrided 4340 steel showing total depth of the layer (diffusion zone).
Gas Nitriding
Nitriding is done typically within temperature range 400-590°C (752-1094°F), which is below Ac1 temperature of the iron-nitrogen system and because of that, it is called ferritic nitriding or just nitriding [1-6]. If processing temperatures exceed the upper temperature range, nitrogen austenite is formed resulting in the presence of an additional sub-layer which its structure depends on the cooling rate [3, 4].
Nitriding Compound Zone (CZ)
The compound zone structure depends on the process parameters and the chemical potential of nitrogen used. The Lehrer diagram describes those parameters and the resultant nitrogen content in iron. Utilizing the Lehrer diagram allows for prediction and control of the amount of nitrogen introduced into the surface of steel [1-6]. At low nitriding potential, CZ is thin or could be completely eliminated, see Fig. 3.
Figure 3
Photomicrograph of the M-50 steel after gas nitriding at very low nitriding potential. Etched with 3% Nital. Note absence of compound zone.
Increase of nitriding potential results in formation of compound zone, which can be quite thick if needed, see Fig. 4.
Figure 4
Photomicrograph of W-2 steel after gas nitriding at a high nitriding potential. Etched with 3% Nital. Note presence of the compound zone (white layer) of significant thickness.
As can be seen above, when nitriding potential is high, thickness of the CZ can be significant and it may contain the Epsilon nitride with the higher nitrogen content. Presence of this nitride accelerates growth rate of the CZ, see Fig. 3 and 4.
Properties of the CZ depend on its structure and the amount of nitrogen in it. Also, as mentioned before, thickness and properties of CZ can be modified by introducing carbon atoms in it.
Nitrocarburizing
Nitriding modified/doped with carbon is for increasing CZ thickness to the range 10-40 µm (0.0004-0.0016”) and formation of Fe3(C, N)1+x phase and the process is called Nitrocarburizing.
The reactivity of the process gases used for gas nitriding and nitrocarburizing treatments is characterized by means of the potentials of nitrogen, carbon, and oxygen, which are defined as nitriding potential, carbon potential, and oxidation potential [3].
Gas Nitrocarburizing
This process is called nitrocarburizing and also FNC (Ferritic Nitrocarburizing) [2]. FNC is an extremally important method of surface hardening for the components made of low-alloy, low-carbon steels although it is quite often also used for other steels when a high hardness as well as excellent corrosion resistance are required. Optimization of the structure for superior corrosion resistance is achieved when both nitriding and carburizing potentials of the nitrocarburizing atmosphere are controlled and when percentages of nitrogen and carbon introduced into Epsilon Layer (Fe2CN) is about [C]/ [N + C] = 0.02–0.2 [3, 6].
Figure 5
Photomicrograph of nitrocarburized 1018 steel. Etched with 3% Nital. Note two sub-layers in the compound zone; the epsilon layer near surface has porosity in it, which may be formed for a purpose of retaining lubricants.
Gas nitrocarburizing shall be carried out in an automated mode, maintaining set parameters of temperature and nitriding with carburizing potentials as recommended by ASM Standard [1]. The process is controlled and maintained automatically at each stage. Recommended values of nitriding and carburizing potentials for temperatures are also listed there.
Nitriding Potential and Carburizing Potentials are defined in the following way:
The nitriding potential is a measure of the nitriding capability of the nitriding atmosphere, which determines the surface nitrogen concentration in iron at a given temperature, and is described by the following equation:
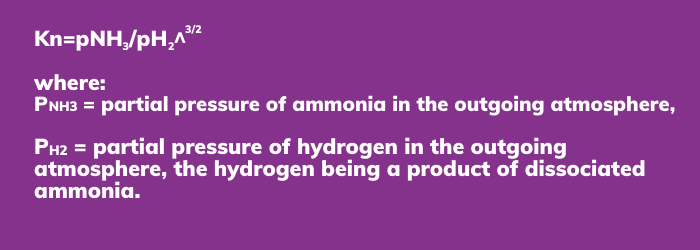
Carburizing Potential
The carburizing potential is a measure of the carburizing capability of the carburizing atmosphere, which determines the surface carbon concentration in pure iron at a given temperature, and is described by either of the two following equations [1]:

The differences between the hardness profiles of nitride layers of unalloyed and alloyed steels are well known. Hardness of diffusion zone in unalloyed steel is very low. Therefore, hardness of the treated component depends on presence of the sufficiently thick compound zone. In situations like that nitrocarburizing is the proper option. It provides sufficient wear protection of the surface. Its corrosion resistance is also very high, much better than resistance of the compound zone produced by nitriding and chromium plating [3, 6].
It should be noted that additional corrosion resistance can be achieved when there is a magnetite oxide layer produced during post-oxidizing step on top of the compound zone [6].
On the other hand, if a good bending and rolling fatigue resistance of the high alloy steels, such as M-50 or 4340 is needed, the best properties are achieved when compound zone is absent or minimized. In those situations, a good diffusion with a high hardness needs to be produced. In those situations, nitriding is used.
In contrast, today, in the case of bath FNC, a deliberate change of the effective chemical potentials of nitrogen and carbon, is still not possible. Therefore, in these processes, the control of the structure of the nitrided case is empirical [3].
Ion Nitriding & Nitrocarburizing
Ion/plasma nitriding and nitrocarburizing is another option for treating ferrous alloys components [7, 8]. This method is excellent when treating very precise parts requiring local protection from the treatment, especially those made of stainless steels or sintered metals. The method is characteristic of a “low-nitriding potential” which allows to limit easily thickness of the compound zone even without very sophisticated control of the process. In many applications, the epsilon type CZ can be produced by doping plasma with methane or other hydrocarbon. Thickness of the compound zone can be limited to not more than 10 µm without loosing all the properties and benefits of such a layer. Those results cannot be obtained so easily when the other methods are used.
Want to Learn More About Nitrocarburizing? Check Out These Other Articles or Give Us a Call at 319-232-5221.
VIEW ADDITIONAL ARTICLES.
Who is Doctor Glow?
Dr. Edward Rolinski, aka Doctor Glow, has been studying the plasma/ion nitriding phenomenon since the 1970s and is arguably one of the most knowledgeable people in North America when it comes to nitriding.
The doctor has written countless articles and whitepapers in industry publications and manuals. Some of his most noteworthy contributions include the chapter on "Controlling Plasma Nitriding" in ASTM International (2017) as well as "Nitriding of Titanium Alloys" in the ASM Handbook (2016).
Dr. Edward Rolinski is the Senior Scientist at Advanced Heat Treat Corp. (AHT) and has been employed at AHT since 1994.
LEARN MORE ABOUT DOCTOR GLOW VIEW HIS RECENT ARTICLES
"When to Use Nitrocarburizing / Nitriding" References
1. “Automated Gaseous Nitriding Controlled by Nitriding Potential”, AMS2759/10B, issued 1999-05, Revised 2018-06, Superseding AMS2759/10A.
2. “Automated Gaseous Nitrocarburizing Controlled by Potentials”, 2018-07, AMS2759™/12, Rev. B.
3. H. J. Spies, A. Dalke, “Case Structure and Properties of Nitrided Steels. In Comprehensive Materials Processing”; Krauss, G., Ed.; Elsevier Ltd., 2014; Vol. 12, p 439–488.
4. E. J. Mittemeijer, “Fundamentals of Nitriding and Nitrocarburizing”, 2013, ASM Handbook, Volume 4A, Steel Heat Treating Fundamentals and Processes, Ed. Dossett and G.E. Totten, editors, pp. 619-646.
5. K. M. Winter, J. Kalucki, “Gas Nitriding and Gas Nitrocarburizing of Steel”, 2013, ASM Handbook, Volume 4A, Steel Heat Treating Fundamentals and Processes, Ed. Dossett and G.E. Totten, editors, pp. 647-679.
6. H. J. Spies, “Corrosion behavior of nitrided, nitrocarburized and carburized steels”, 2014, Thermochemical Surface Engineering of Steels, Ed. Eric J. Mittemeijer and Marcel A. J. Somers, Published by Elsevier Ltd., Pp. 267-305.
7. E. Rolinski,” Plasma Assisted Nitriding and Nitrocarburizing of Steel and other Ferrous Alloys”, Chapter 11 in Thermochemical Surface Engineering of Steels, Ed. E. J. Mittemeijer and M. A. J. Somers, Pub. Woodhead Publishing, 2014, pp 413-449.
8. “Ion Nitriding”, AMS2759™/8, Rev. B, Revised 2018-06, Superseding AMS2759/8A.
- edward rolinski
- ferritic nitrocarburizing
- gas nitriding
- ion nitriding
- nitriding
- nitrocarburizing
- plasma nitriding